Skilled packaging machine repair service for industrial needs.
Skilled packaging machine repair service for industrial needs.
Blog Article
How Expert Packaging Device Repair Work Services Lessen Downtime and Boost Performance
Professional packaging equipment repair work services are vital in minimizing downtime and improving performance via specialized diagnostics and timely treatments. The implications of such solutions expand past immediate repair work-- unloading the broader effect on functional efficiency discloses important understandings into lasting productivity methods.
Value of Timely Repair Works
Prompt repair services of product packaging machines are critical for preserving operational effectiveness in any kind of production setting. When machinery malfunctions or breaks down, it can result in considerable disturbances in assembly line, leading to raised downtime and lost revenue. The longer a packaging equipment stays out of commission, the higher the effect on overall performance, potentially triggering delays in fulfilling orders and reducing customer satisfaction.
Along with the prompt economic effects, postponed repairs can cause a lot more substantial damages to the equipment. Elements that are not addressed quickly can weaken even more, requiring even more costly repair services or total replacements, which can have been avoided with timely treatment. Regular upkeep and punctual repairs can boost the life expectancy of product packaging devices, ensuring that they run at ideal performance degrees.
Buying specialist packaging maker repair service services is essential for alleviating these risks. A positive method to fixings not only keeps production timetables yet additionally fosters a society of integrity within the organization. By focusing on prompt repairs, services can maintain their one-upmanship, maximize resource appropriation, and eventually boost their profits via improved functional efficiency.
Knowledge in Diagnostics
When it pertains to preserving the performance of product packaging machines, competence in diagnostics plays a pivotal duty in determining problems before they intensify into major failures. Experienced professionals make use of innovative analysis tools and methods to do detailed assessments of equipment performance. This positive method allows them to identify the origin of malfunctions, whether they stem from mechanical wear, electrical faults, or software disparities.
Reliable diagnostics not only help with swift identification of troubles yet likewise improve the general integrity of product packaging operations. By performing thorough analyses, specialists can assess the wellness of crucial parts, making sure that even small abnormalities are addressed quickly. This attention to detail reduces the threat of unforeseen malfunctions, which can bring about costly downtime.
In addition, professional diagnostics provide beneficial insights into operational patterns, allowing services to make informed choices concerning equipment upgrades or alterations. By leveraging these insights, firms can maximize their product packaging procedures, leading to enhanced efficiency and efficiency. Inevitably, investing in diagnostic proficiency is crucial for organizations looking for to preserve smooth procedures and promote high standards of high quality in their product packaging processes.
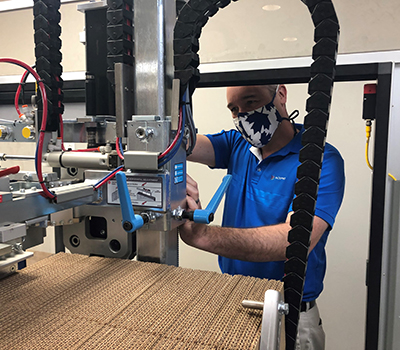
Preventive Upkeep Benefits
Precautionary upkeep matches specialist diagnostics by proactively attending to potential problems prior to they show up into major issues. By applying a structured precautionary upkeep program, firms can considerably lower the risk of unanticipated machine failures, thus lessening pricey downtime. Normal assessments, cleaning, and parts replacement help guarantee that product packaging equipment operates at optimum performance.
Among the vital advantages of preventative upkeep is its capability to extend the lifespan of equipment. By frequently keeping equipment, businesses can avoid the intensifying results of wear and tear helpful resources that often bring about major repair work or substitutes. This not just conserves funding but additionally boosts the overall dependability of production procedures.
Additionally, precautionary maintenance adds to enhanced safety problems within the office. By determining and correcting prospective dangers before they escalate, companies develop a more secure setting for their staff members (packaging machine repair service). This aggressive method not only shields employees but additionally promotes a culture of duty and watchfulness
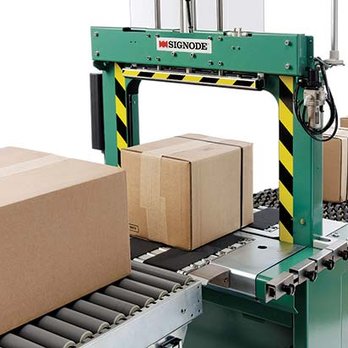
Personalized Solution Solutions
Recognizing the distinct demands of each business, personalized solution solutions for packaging maker repair offer tailored techniques that enhance functional performance. These solutions are developed to attend to details challenges faced by various markets, making certain that machine downtime is minimized and productivity is maximized.
Expert repair service services begin with a company website detailed analysis of a firm's product packaging procedures. By recognizing the specific machinery included and the needs of the manufacturing atmosphere, technicians can develop a customized maintenance and fixing strategy. This might consist of specialized training for in-house personnel, the application of predictive maintenance innovations, or the arrangement of specialized support during optimal manufacturing times.
Furthermore, tailored options can include versatile service agreements that straighten with a firm's operational routine, allowing for repairs to be executed throughout off-peak hours. By focusing on the special requirements of each company, these custom options ensure that repairs are not just efficient however also flawlessly integrate into existing operations.
Eventually, the focus on personalization enables firms to enhance their packaging procedures, causing boosted dependability and performance of machinery, which is vital for preserving competitive benefit in today's fast-paced market.
Influence On Overall Performance
Customized service options not only address certain repair requirements however also play a substantial function in enhancing general functional effectiveness. By giving targeted interventions, specialist product packaging equipment repair work solutions straight decrease the regularity and duration of tools failures. This aggressive method makes certain that assembly line stay functional, minimizing interruptions that can lead to pricey downtime.
Moreover, effective fixing solutions add to smoother operations, Get More Information as well-maintained equipment operates at ideal efficiency degrees. When machines work properly, the top quality of packaged items improves, resulting in less flaws and much less rework. This improvement not only improves productivity yet additionally reinforces customer fulfillment.
In enhancement, normal upkeep and quick action times from fixing specialists cultivate a society of integrity within the organization. Workers can focus on their key jobs instead of stressing concerning possible tools failures. The overall throughput of the manufacturing procedure rises, enabling business to meet demand much more successfully.
Eventually, the tactical investment in specialist repair service services equates to improved efficiency across all operational elements, making certain that services can adapt and thrive in an affordable market. This synergy between upkeep and efficiency is vital for long-term success.
Verdict
In verdict, professional packaging equipment repair work services play an essential duty in decreasing downtime and enhancing efficiency within making environments. Timely repair services, specialist diagnostics, and preventative maintenance add to the integrity of equipment, while customized service options resolve specific functional needs.
Report this page